Digital Work Instructions are developed using intuitive software that allows manufacturers to create detailed, step-by-step instructions.
The Power of Digital Work Instructions in Modern Manufacturing
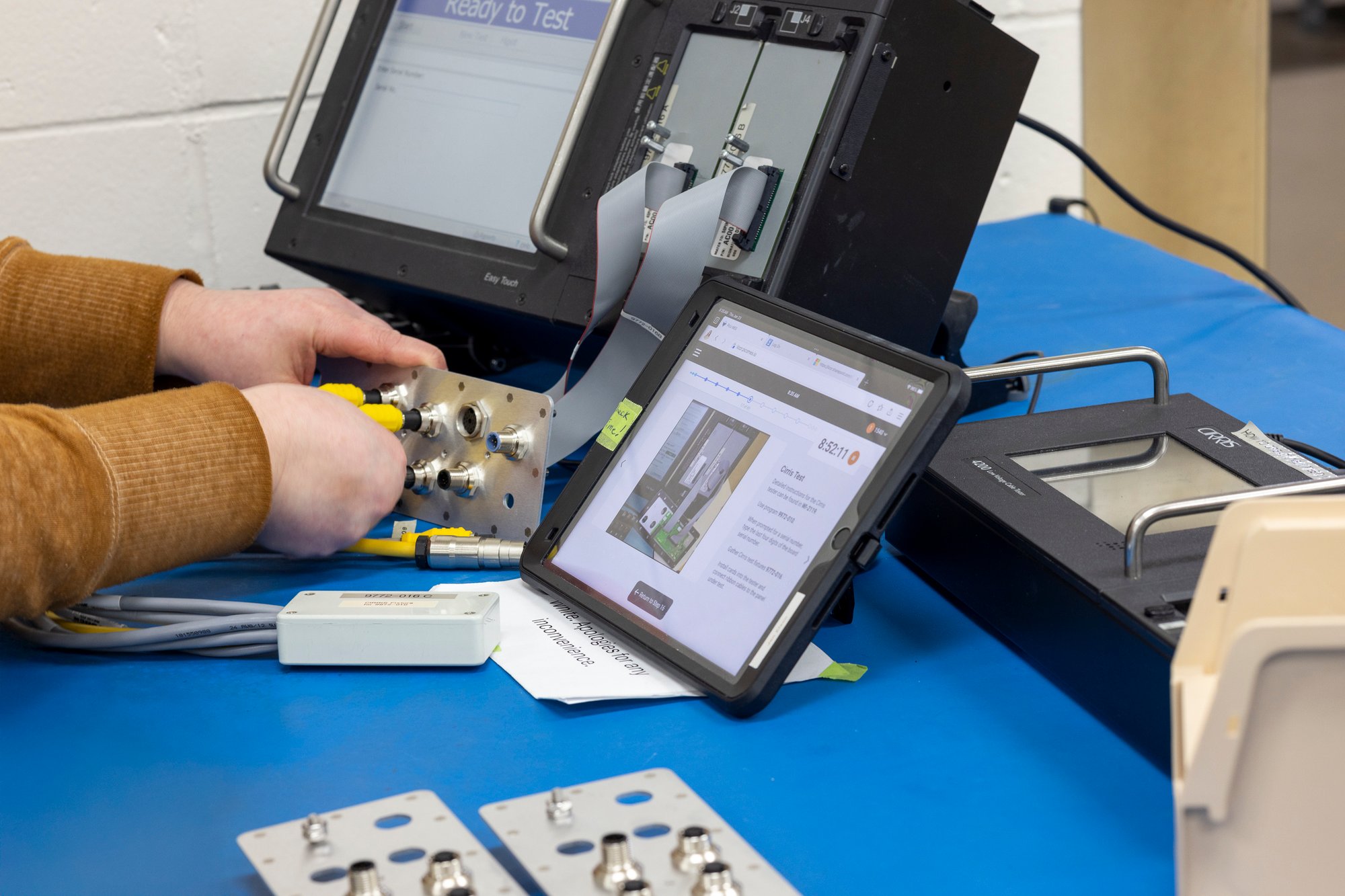
01
Identify Error-Prone Areas
Pinpointing the areas most susceptible to errors is the foundation for a successful error-proofing strategy.
- Conduct a Production Audit
Begin by analyzing production data, quality control reports, and incident logs to identify recurring issues. Are there specific steps or stations where defects frequently occur? Focus on both human and machine-related errors. - Involve Frontline Workers
Your factory workers are often the first to detect potential problems. Encourage them to share insights about where and why errors happen. Their feedback can reveal valuable information that might not be captured in data alone. - Use Root Cause Analysis (RCA)
Addressing the surface issue isn’t enough. Use tools like 5 Whys or Fishbone diagrams to trace errors back to their origin. This ensures that you’re solving the root causes of mistakes, not just treating the symptoms. - Identify High-Risk Processes
Prioritize error-proofing efforts in processes or stations where errors are both frequent and costly. In industries like aerospace or medical device manufacturing, even small mistakes can have severe consequences, making these areas critical candidates for error-proofing.
02
Choose the Right Tools for Your Needs
Once you’ve identified the most error-prone areas in your process, it’s time to select the right error-proofing tools and technologies that can help address those specific issues. It’s important to remember that there’s no one-size-fits-all solution, as different processes and error types require different tools.
- Evaluate Existing Solutions
Review the tools already in place. Are manual checks being used where automation could improve accuracy? Are physical poka-yoke devices still effective, or are they outdated? - Consider the Nature of Errors
- For human errors: If your issues stem from human mistakes (e.g., incorrect assembly or missing parts), consider digital solutions like real-time visual prompts, guided instructions, or automated feedback systems that alert workers when errors occur.
- For machine-related errors: If machines are responsible for frequent errors, automated quality checks and real-time equipment monitoring can prevent downtime and ensure consistency.
- Decide on Digital or Physical Error-Proofing
Traditional error-proofing methods rely on mechanical devices like jigs or limit switches. While effective, these tools are reactive. Modern error-proofing systems provide digital solutions that are more flexible and scalable. For instance, PICO’s real-time monitoring and error-detection software helps you respond to shop floor issues faster and make quicker decisions, enabling manufacturers to adapt effectively to changing conditions.
03
Pilot the Process on a Small Scale
Before rolling out your error-proofing solution across the entire production line, it’s best to pilot it in a controlled environment. A pilot allows you to test the effectiveness of your tools, make necessary adjustments, and build confidence before full-scale implementation.
- Select a Pilot Area
Choose a station, line, or product to test your error-proofing tools. Ideally, this should be an area that experiences frequent or costly errors, based on the findings from Step 1. - Set Clear Objectives
Establish measurable goals for the pilot. For example, you might aim to reduce defects by a specific percentage or minimize rework time. Defining these metrics upfront will help you evaluate the success of the pilot and guide future rollouts. - Monitor Performance Closely
During the pilot, track error rates, production efficiency, and worker feedback to gauge how well the tools are functioning. Take note of any issues or challenges that arise, as these can inform improvements in broader implementation. - Be Open to Iteration
Piloting is an iterative process. Expect to discover areas for improvement, and be ready to adjust your system based on feedback. This phase allows you to refine the approach, ensuring maximum effectiveness during full-scale rollout.
04
Train and Support Your Team
Technology alone can’t drive error-proofing, your team’s understanding and buy-in are equally important. Proper training and ongoing support are crucial for success.
- Design Hands-On Training
Provide hands-on training to your workers. For instance, if you’re implementing PICO’s real-time error detection system, ensure employees practice using digital prompts and alerts in their day-to-day tasks. - Provide Continuous Learning Resources
Equip workers with digital resources like video tutorials, interactive guides, and quick-reference materials to reinforce training. Modern error-proofing systems like PICO offer real-time prompts and instructions, making it easier for workers to adapt. - Encourage Ownership and Accountability
Employees are more likely to engage with error-proofing initiatives when they feel a sense of ownership. Encourage them to identify potential errors in their processes and suggest improvements. Establishing a feedback loop where workers can share their experiences ensures continuous improvement. - Support Cross-Functional Training
Cross-functional training builds a more resilient workforce. When employees understand the full production process, they’re better equipped to spot errors before they occur.
05
Monitor and Optimize the System Continuously
Error-proofing isn’t a set-it-and-forget-it solution. Continuous monitoring and optimization are key to long-term success.
- Use Data to Drive Improvements
Modern error-proofing systems like PICO’s provide real-time data on production efficiency and error trends. Use these insights to make data-driven decisions about where further improvements are needed. - Regularly Audit Error Rates
Conduct regular audits to track error rates, defect occurrences, and rework data. Are certain errors still slipping through? Are there areas where performance has improved dramatically? Use this data to tweak your systems for optimal performance. - Adapt to Changing Conditions
Manufacturing environments are constantly evolving. Whether it’s new equipment, changing product lines, or shifts in workforce dynamics, your error-proofing tools should be flexible enough to adapt.. - Solicit Continuous Feedback
Encourage workers and managers to offer ongoing feedback about how error-proofing tools are functioning. Are there frustrations or gaps that need to be addressed? Continuous feedback is essential to evolving your system as conditions change. - Benchmark Your Progress
Compare performance data before and after error-proofing implementation to measure improvement. Benchmarking your progress not only demonstrates the ROI of your investment but also ensures ongoing refinement of your systems.
In manufacturing, success comes down to how well materials, machinery, tools, and people work together. When one part of this system falls out of sync, it creates a ripple effect that’s felt across the entire operation, slowing productivity, affecting quality, and increasing costs.
Many manufacturers digitize their shop floor to mitigate these risks, moving away from outdated, paper-based instructions. But there are still manufacturers who cling to outdated methods. Perhaps it’s because they see digital work instructions in the literal sense. And while that’s partly true, digital work instructions go beyond simply being digital versions of paper manuals. They are interactive tools that help people and processes operate better. They bridge gaps in knowledge, reduce errors, and support continuous improvement so that every part of the system stays in sync.
In this article, we’ll break down what Digital Work Instructions are, how they function, and the practical ways they can improve manufacturing operations.
What Are Digital Work Instructions?
Digital Work Instructions are more than just work instructions, quality manuals, and standard operating procedures (SOPs) stored online. They are dynamic tools designed to keep operations synchronized, addressing the very ripple effects that occur when processes fall out of sync. By moving them to a digital platform, manufacturers create a single source of truth—providing operators with clear, step-by-step guidance to perform tasks accurately and consistently.
But being a central repository for work instructions isn’t all Digital Work Instructions can do. They offer features like real-time updates, visual aids, standardization, customization, and accessibility. These features enable operators to:
- Instantly push updates across multiple devices, ensuring everyone has the latest information.
- Access instructions enriched with images and diagrams to simplify complex tasks.
- Customize workflows to fit specific products, processes, or skill levels, enhancing both flexibility and consistency.
With these capabilities, Digital Work Instructions don’t just share information—they actively support continuous improvement, reduce errors, and help every part of the manufacturing system stay connected and efficient.
Key Benefits of Digital Work Instructions
When one part of a manufacturing system falls out of sync, it can create disruptions in productivity, quality, and costs. Digital Work Instructions are designed to prevent these disruptions by keeping people, processes, and tools aligned.
Here’s how they make a measurable difference:
Improve Efficiency
Clear, concise instructions eliminate guesswork. Operators no longer waste time searching through manuals or seeking clarifications—they can take immediate action, keeping workflows smooth and consistent.
Ensure Faster, More Effective Training
Visual aids like diagrams and videos make training intuitive. New operators can quickly grasp complex tasks without relying on lengthy manuals, reducing onboarding time and ensuring consistency across teams.
Capture Expert Knowledge
As experienced workers retire, Digital Work Instructions capture critical know-how in a central system. This ensures that essential processes are preserved and easily passed on to new team members, preventing knowledge gaps that could slow down operations.
Reduce Chances of Human Error
Errors often stem from unclear instructions or hard-to-follow processes. Digital Work Instructions provide up-to-date, easy-to-understand guidance with visual aids that reduce the risk of misinterpretation and human error. For example, in electronic assembly, operators can rely on clear diagrams and real-time alerts to ensure proper wiring connections, preventing costly mistakes.
Boosting Productivity
Real-time updates eliminate downtime caused by outdated instructions. Operators always have the latest information at their fingertips, enabling faster problem-solving and seamless communication.
Improved Employee Performance
Clear, visual instructions give employees the confidence to handle complex tasks effectively.
Digital work instructions also support continuous learning, helping employees build skills over time and improving overall performance on the shop floor.
Cost Savings
Digital Work Instructions reduce costs by eliminating the need for printed manuals, minimizing errors that cause equipment damage, and decreasing downtime.
Attracting and Engaging the Next Generation of Talent
For Millennials and Gen Z, digital tools signal a modern, forward-thinking workplace. Adopting Digital Work Instructions shows that your shop floor embraces digital transformation, making way for tools that reduce the learning curve, enhance employee engagement, and support continuous growth.
How Digital Work Instructions Work
Digital Work Instructions are designed to fit seamlessly into daily operations, making tasks simpler and processes more efficient. Their value comes from how they’re created, implemented, and how they’re used on the shop floor. Here’s how they work:
2. Deployment:
Once created, Digital Work Instructions are viewable across tablets and monitors. All revisions and updates are in real-time, so the production floor has access to the latest instructions wherever they’re needed.
3. Real-Time Application:
On the shop floor, operators interact with Digital Work Instructions as they complete tasks like assembly, quality checks, and troubleshooting.
4. Feedback and Continuous Improvement:
Digital Work Instructions aren’t static. Operators can provide feedback, and performance data can highlight areas for improvement, helping refine processes over time.
“There isn’t a training gap; the quality of work we produce no longer depends on the trainer or trainee because Pico’s software eliminates variability.”
Maurice Stallard, Director of Engineering & Manufacturing, HJI Supply Chain Solutions
Is It Time to Upgrade Your Work Instructions?
If you’re wondering whether your current work instructions are holding you back, here’s a quick diagnostic to help you decide:
- Are your operators frequently making errors due to unclear instructions?
- Do process updates take too long to implement on the shop floor?
- Is onboarding new operators slow or inconsistent?
- Are you struggling to maintain compliance or traceability during audits?
- Do you rely heavily on paper manuals or static documents that are hard to update?
If you answered “yes” to any of these questions, it might be time to consider transitioning to Digital Work Instructions. Work instructions captured in a Word document, Powerpoint, or 2D engineering drawings often fail to keep up with the evolving demands of modern manufacturing. They’re often static, hard to update, and prone to misinterpretation, leading to errors, wasted time, and higher costs. Digital Work Instructions solve these problems by offering real-time updates, clear visuals, and easy access—helping manufacturers stay efficient and audit-ready.
Digital Work Instructions vs. Manual Work Instructions
Feature |
Digital Work Instructions |
Manual Work Instructions |
---|---|---|
Ease of Updates |
Updates are in real-time with version control and authorization built-into the software. | Updates are manual and time-consuming, often leading to outdated materials on the shop floor. Updating work instructions is often the most dreaded part of an engineer’s job. |
Enhanced Clarity |
Includes colorful visual aids like images, videos, and diagrams, making complex processes easy to understand and reducing errors. | Lacks visual guidance, making complex processes harder to follow and increasing the risk of errors. |
Error-Proofing |
Checks and balances are built into the software, so operators are not allowed to proceed unless certain steps have been performed to specification. | No built-in error-proofing measures. Errors are not caught until end-of-line testing or even worse, warranty claims and customer complaints. |
Flexibility for Variations | Handles high product variation through templates and process variants, enabling efficient workflows in complex environments. | Managing variations or rework requires significant manual effort, slowing production. |
Real-World Applications of Digital Work Instructions
Digital Work Instructions are versatile and can improve processes wherever there’s a need for clear, consistent guidance. Here’s how Digital work instructions make a difference across various manufacturing environments:
Automotive Industry
Digital work instructions help ensure precision in automotive manufacturing. With detailed step-by-step instructions with images, diagrams, and videos, complex tasks like engine assembly become easier as operators can meet exact specifications, reduce errors, and improve product reliability.
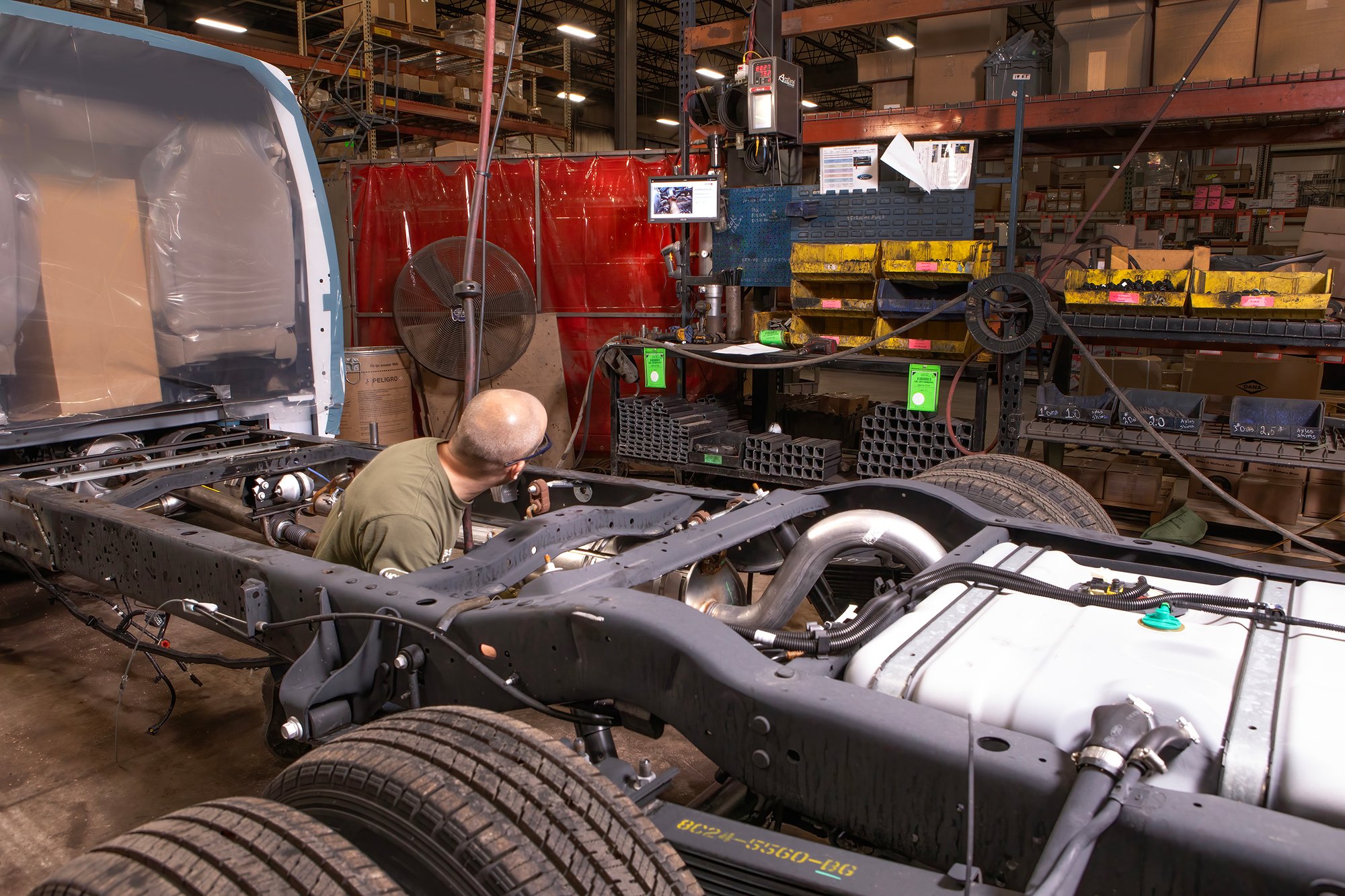
Electronics Manufacturing
When dealing with intricate wiring and soldering, there’s little room for mistakes. Digital work instructions use visual aids and real-time validation to guide operators through each step, reducing errors and minimizing costly rework.
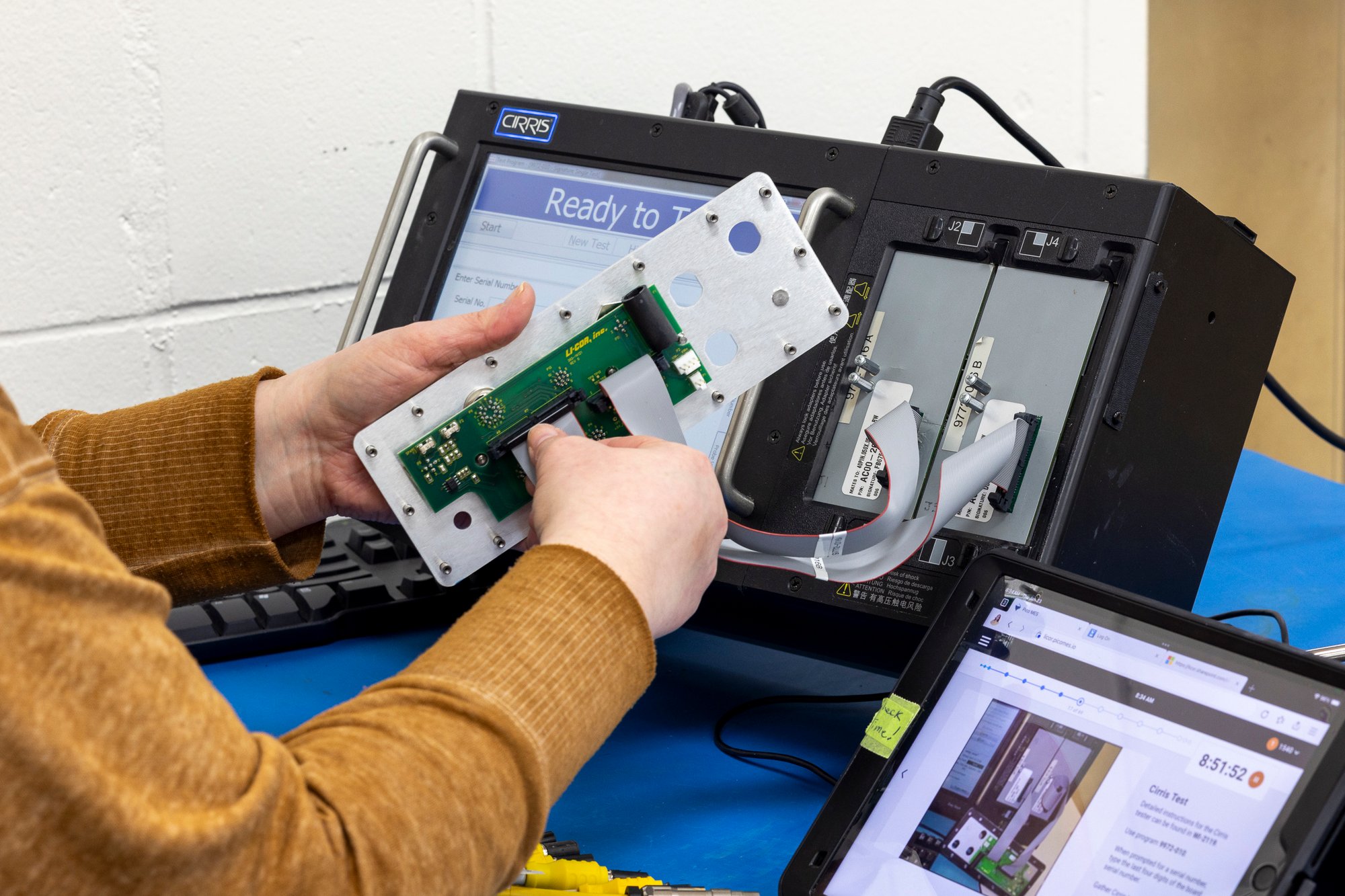
Assembly Processes
Digital work instructions simplify multi-step assembly tasks by offering clear, interactive visual guides. For example, in box build assembly, operators can easily follow the correct sequence, ensuring accuracy and consistency from start to finish.
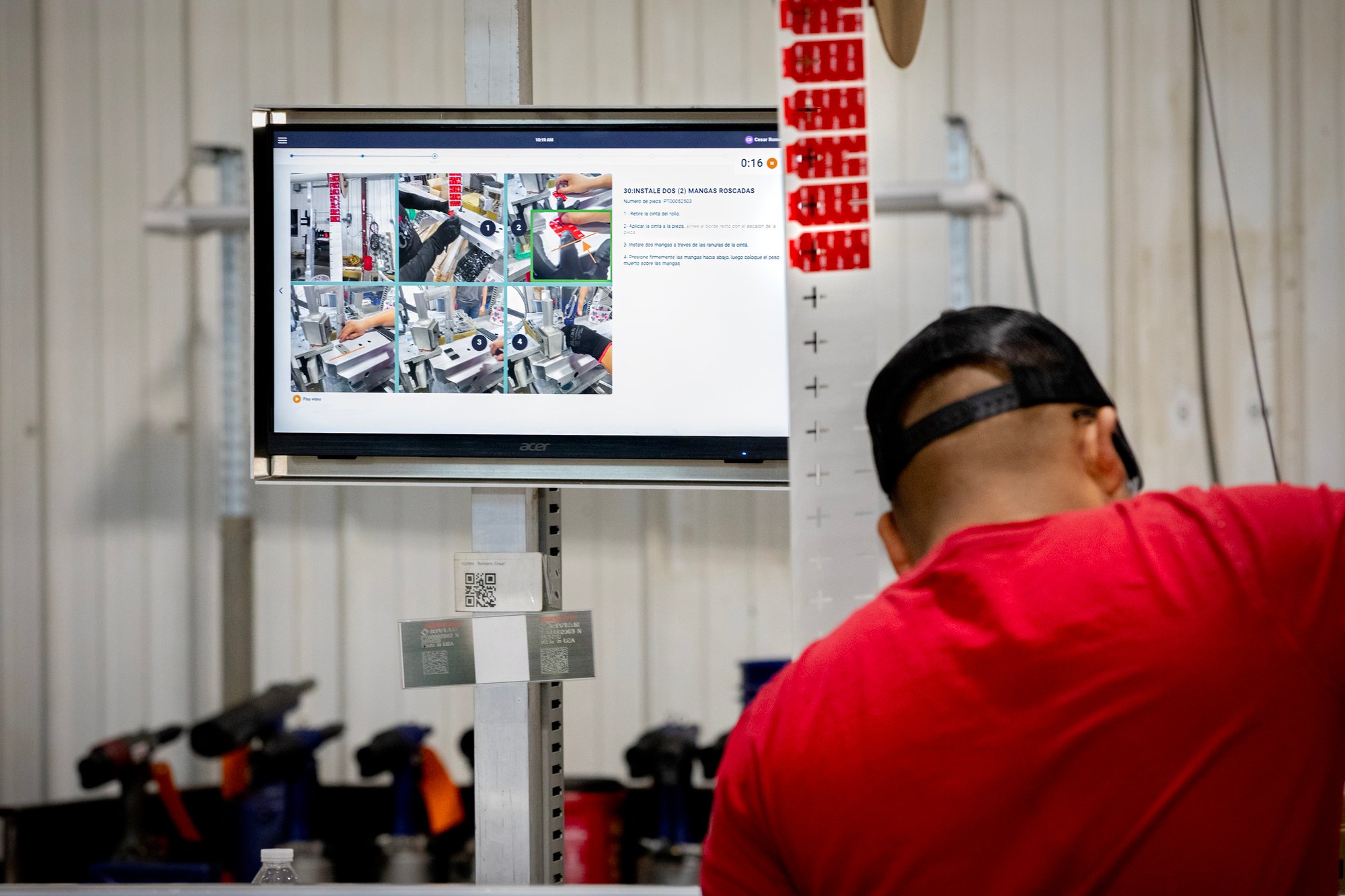
Quality Control
Standardizing inspection procedures is key to maintaining product quality. Digital Work Instructions help inspectors follow consistent protocols, making it easier to meet compliance requirements and ensure every product meets high standards.
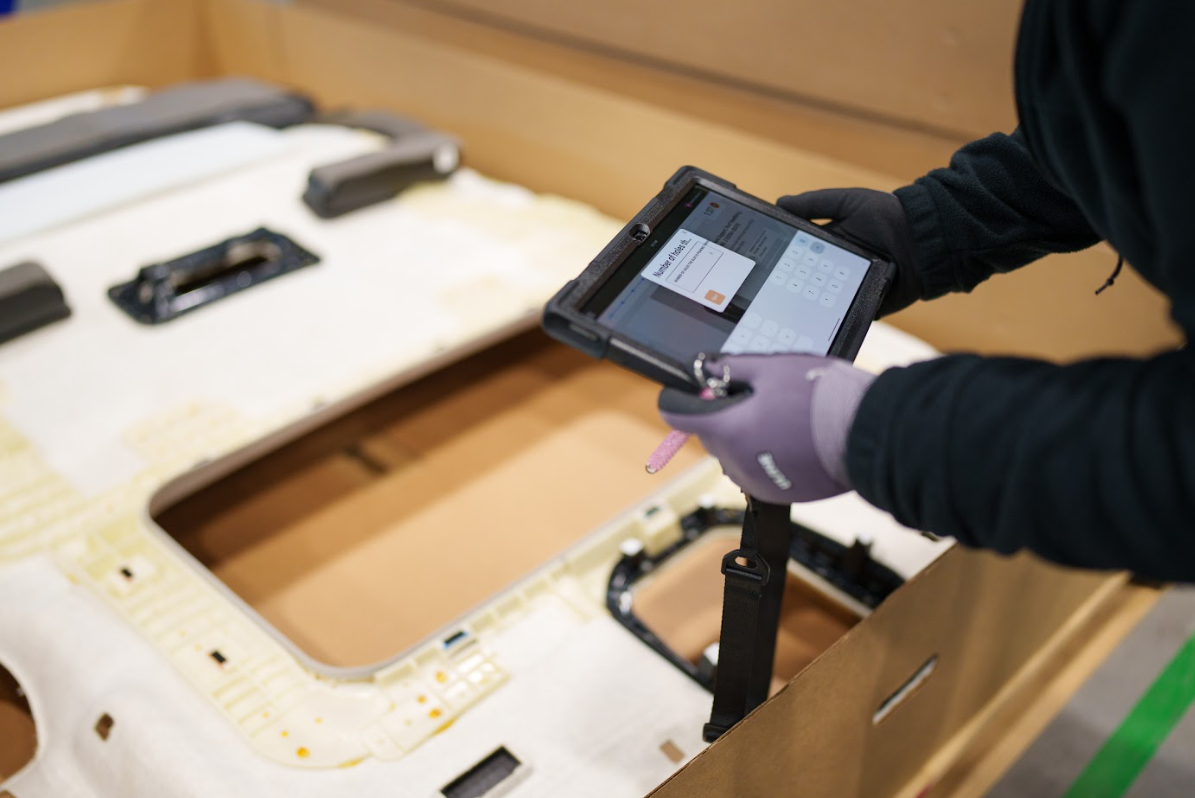
High-Mix, Low-Volume Production
For manufacturers handling diverse product variations, Digital Work Instructions offer adaptable templates that streamline process changes. This flexibility saves time, reduces errors, and ensures consistency across custom configurations.
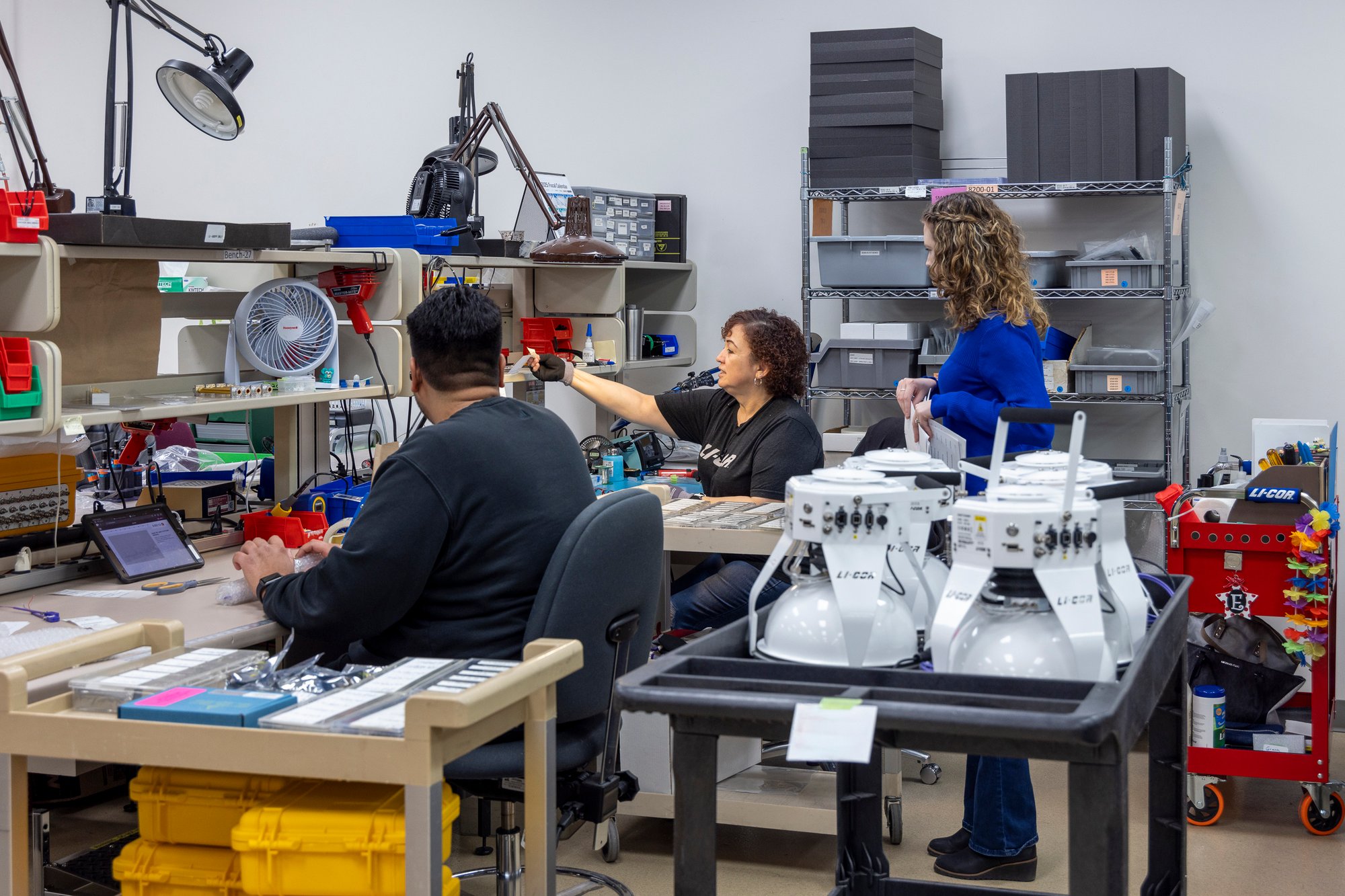
How PICO Can Help
PICO makes it easy to bring Digital Work Instructions to your shop floor. With smart, user-friendly features and seamless integration, PICO ensures Digital Work Instructions deliver maximum impact. Here’s how:
- Seamless Integration: Works with over 200 shop floor tools and devices, fitting into your existing setup without hassle.
- Just like PowerPoint - but Better and Faster: Modeled after familiar tools like PowerPoint and Google Slides, work instructions are easy to create, revise, and maintain. Change control and user management is built into the system.
- Advanced Operator Guidance: Interactive features like color-coded alerts, step-by-step instructions, and layered content , guide operators through even the most complex tasks.
- Error-Proofing Tools: Built-in validation mechanisms reduce defects and rework, ensuring quality and consistency.
- Scalability for SMBs: PICO offers a free entry-level solution, making it easy for businesses to get started with Digital Work Instructions. As operations expand, flexible pricing plans allow manufacturers to scale up seamlessly, ensuring they can grow without limitations.
- Comprehensive Analytics: Gain insights into Digital Work Instructions usage and production performance to optimize workflows and make data-driven decisions.
''Great entry point—an intuitive, modular system that's easy to adopt. The cost is very reasonable for small companies."
Glenn H., Director of Process Development
By leveraging PICO’s platform, manufacturers can maximize the benefits of Digital Work Instructions, empowering their workforce and staying ahead in an ever-evolving industry.
Build a Smarter, More Productive Shop Floor
Digital Work Instructions are practical tools that go beyond digitalizing manuals. They help improve efficiency, reduce errors, and help operators get the job done right the first time.
Ready to see how Digital Work Instructions can make a real difference? Schedule a demo with PICO today and discover practical ways to streamline your shop floor.
Frequently Asked Questions (FAQs)
How quickly can Digital Work Instructions be implemented on the shop floor?
PICO’s digital work instructions can be instantly accessed via cloud and an on-premise deployment takes a few hours, at most. The software is designed for rapid deployment, with minimal IT requirements. Most manufacturers can integrate Digital Work Instructions and start seeing results within days, not weeks.
Do Digital Work Instructions require extensive IT resources to maintain?
No, PICO’s streamlined infrastructure ensures that Digital Work Instructions are easy to manage without heavy IT involvement. Updates can be made instantly across all devices without the need for complex configurations.
Are Digital Work Instructions affordable for small and mid-sized manufacturers?
Yes, PICO offers scalable solutions tailored to SMBs, including a free entry-level option. Manufacturers can start small and expand as their needs grow, ensuring cost-effectiveness.
How do Digital Work Instructions support quality assurance and compliance?
Digital Work Instructions document every step of the production process, creating a detailed build history. This ensures traceability, supports audits, and helps manufacturers meet regulatory requirements with confidence.
Can Digital Work Instructions manage high product variation?
Yes, Digital Work Instructions are specifically designed to handle high product variation by enabling quick customization of instructions for different configurations or components, ensuring efficiency in high-mix, low-volume environments.
Can Digital Work Instructions improve workflows for rework processes?
Yes, Digital Work Instructions allow operators to revisit earlier steps to perform rework efficiently without disrupting overall workflows. This feature ensures quality corrections can be handled seamlessly.
How do Digital Work Instructions manage version control and updates?
PICO’s Digital Work Instructions include a built-in version control and approval process, ensuring all instructions are accurate and up to date. Updates are deployed instantly across devices for seamless operator access.
Gain access to hundreds of solutions from a single platform
Step into the future of factory operations with Pico MES. Start your journey toward a more efficient, error-proof factory floor today.
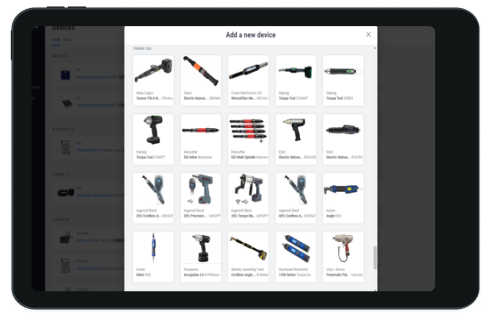